Understanding Polymer Clay
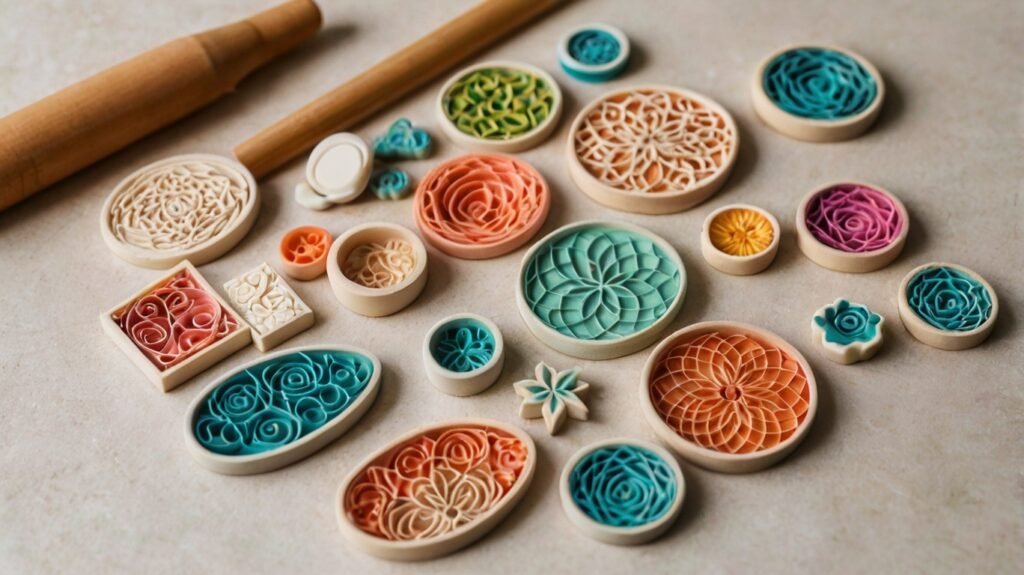
Polymer clay is a versatile modeling material composed primarily of polyvinyl chloride (PVC) combined with various additives that give it unique properties. This synthetic medium is favored by artists, crafters, and hobbyists due to its ability to be molded into intricate shapes and forms. Once shaped, polymer clay can be baked in a conventional oven to harden and set, making it suitable for a wide range of craft projects.
There are several types of polymer clay available on the market, each designed for specific applications and projects. The most recognized brands include Sculpey, Fimo, and Premo, all of which offer various formulations with differing textures, flexibility, and finish. For instance, some polymer clays are softer and more pliable, allowing for finer detail work, while others provide a firmer consistency, which is better for creating larger sculptures. Artists often choose a type based on their desired finish, ease of use, and the specific characteristics they need for their projects.
Polymer clay’s properties extend beyond mere malleability; it can mimic a multitude of materials, including wood, stone, and glass, thanks to its ability to be tinted and layered. This adaptability makes it particularly popular in jewelry making, where artisans create unique pieces ranging from buttons to intricate pendants. Additionally, it is frequently employed in modeling, where artists can craft figurines, dolls, and miniature scenes with remarkable detail. The uses of polymer clay are virtually limitless, and its relatively low cost, coupled with its ease of accessibility, makes it an appealing option for both beginners and experienced crafters alike.
The Importance of Polymer Clay Cutters
Polymer clay cutters play a crucial role in the art and craft of working with polymer clay, an incredibly versatile medium favored by both amateur and professional artisans. These specialized tools enable crafters to create precise shapes and intricate designs, elevating their projects beyond simplistic forms. When using polymer clay, the ability to achieve consistent and uniform shapes is essential for producing appealing finished pieces, and cutters serve this purpose exceptionally well.
One of the primary advantages of using polymer clay cutters is the efficiency they bring to the crafting process. Hand-cutting clay can be time-consuming and may yield inconsistent results. However, with a wide range of shapes and sizes available, polymer clay cutters allow artists to produce multiple identical pieces in significantly less time. This efficiency not only streamlines the creative process but also enhances the overall productivity of projects, making it easier for crafters to meet deadlines or fulfill customer orders.
Moreover, the use of polymer clay cutters contributes to design uniformity, an essential factor when creating collections or series of pieces. By employing the same cutter across various works, artists can ensure that their creations maintain a coherent aesthetic, which is vital for branding and showcasing an art style. Cutters also allow for intricate detailing that might be challenging to achieve through freehand methods, providing endless opportunities for creativity and innovation.
Craft enthusiasts can choose from an extensive selection of designs, from simple geometric shapes to complex decorative elements, ensuring that their artistic endeavors are only limited by their imagination. In summary, polymer clay cutters are invaluable tools that empower artists and crafters to work efficiently while maintaining consistency and precision in their designs.
-
Handmade Strawberry Jam Jar Earrings – K-Pop Inspired 🍓 Luxury Fruit Edition | Customized Indian Jewelry 🍓
Original price was: ₹999.00.₹699.00Current price is: ₹699.00.set -
Resin Handmade Love Valentine Cup Set with Heart – Bling On
Original price was: ₹1,299.00.₹899.00Current price is: ₹899.00.set -
“Floral Bliss” ECO-Resin Ring Holder – Trending Jewelry Display (Wedding Special) 🌸
Original price was: ₹899.00.₹699.00Current price is: ₹699.00.
Types of Polymer Clay Cutters
Polymer clay crafting is a versatile and creative practice, and having the right tools can significantly enhance the crafting experience. One of the essential tools for working with polymer clay is the cutter. Various types of polymer clay cutters are available, each serving unique functions that cater to different crafting needs. Understanding these types can help artisans choose the ideal cutter for their projects.
The first group of cutters is cookie cutters, which are commonly used in the polymer clay community. These cutters come in numerous shapes and sizes, making them perfect for creating flat shapes and designs. They are typically made from metal or plastic and can easily imprint shapes onto the clay. Due to their affordability and variety, cookie cutters are popular among both beginners and experienced crafters.
Another type is the plunger cutter, which features a customizable plunger mechanism that pushes out the clay after cutting. Plunger cutters are especially beneficial for creating intricate designs, as they can easily release the clay without distorting its shape. This functionality makes them a favored choice for creating thin and delicate motifs, such as flowers and leaves.
Blade cutters, often referred to as craft knives, provide artisans with the ability to create more detailed and specific cuts. They come in various shapes and sizes, allowing for intricate designs and precise detailing. Blade cutters are indispensable for tasks such as slicing, trimming, and carving polymer clay. Their versatility makes them one of the most valuable tools for advanced polymer clay projects.
Lastly, custom-shaped cutters offer unique designs that may not be found in standard cutter sets. Crafters can find or create their own custom shapes, which can be essential for themed projects or personal branding of clay creations. By utilizing these different types of polymer clay cutters, artisans can unlock their creativity and produce unique and impressive works of art.
The Rise of 3D Printed Cutters
The advent of 3D printing technology has significantly altered the landscape of various crafting communities, including that of polymer clay enthusiasts. In recent years, the popularity of 3D printed cutters has surged, providing artists with innovative tools to push the boundaries of their creativity. Unlike traditional metal or plastic cutters, which may offer limited shapes and designs, 3D printed cutters can be tailored to meet specific artistic needs, resulting in unique creations that were previously unattainable.
One of the primary advantages of 3D printed cutters is their ability to facilitate custom designs. With software capable of generating complex shapes, a designer can take a concept from imagination to physical form with relative ease. This flexibility not only enables the creation of intricate patterns but also allows users to replicate personal symbols, logos, or themes in their polymer clay projects. Furthermore, the accessibility of 3D printing technology means that artists can produce their own cutters at home, allowing for a more personalized crafting experience.
In addition to customization, 3D printed cutters often present a more affordable option for hobbyists. Traditional cutters can be costly, especially when seeking specific shapes or sizes. In contrast, once an artist acquires the necessary 3D printing equipment, the cost of producing new designs can be significantly lower. This democratization of cutter production caters to a broader audience, making unique and tailored polymer clay tools accessible to all levels of artisans, from beginners to professionals.
Moreover, 3D printed materials are continually improving, leading to enhancements in durability and ease of use. Advanced thermoplastic filaments offer strong yet lightweight options, ensuring that these custom cutters remain functional over time. As the technology evolves, the polymer clay community can expect further innovations that will elevate the crafting experience. Embracing 3D printed cutters not only fosters creativity but also signifies a transformative shift in how artisans approach their projects.
Choosing the Right Cutter for Your Project
Selecting the appropriate cutter for your polymer clay project is crucial to achieving the desired results. The choice of cutting tools significantly affects the precision, efficiency, and overall outcome of your crafted items. Therefore, several factors should be considered to ensure the cutter you choose aligns well with your project’s unique requirements.
First and foremost, the size of the cutter plays a vital role. Assess the scale of your project to determine whether you require a small, intricate cutter for detailed designs or a larger cutter for broader shapes. For instance, if you’re working on delicate ornaments, opting for smaller cutters will allow for greater accuracy, whereas larger shapes would benefit from bigger cutters, which can simplify the process.
Next, consider the shape of the cutter. There is a vast array of shapes available, from geometric forms to more elaborate designs. The shape should reflect the specific elements of your project. If you aim to create floral designs, for example, floral cutters or cutters shaped like leaves will enhance the consistency and aesthetics of your work. Aligning the shape of the cutter with the intended design will yield more cohesive results.
The material of the cutter is another significant aspect to keep in mind. Polymer clay cutters come in various materials such as plastic, metal, and silicone. Each material has distinct properties that affect the cutting experience. Metal cutters tend to provide sharper, cleaner edges, while plastic options are lightweight and often easier to handle. Consider the type of polymer clay being used and select a cutter that will complement it effectively.
Lastly, the cutting technique is essential. Different techniques may require different kinds of cutters. If you plan on using detailed techniques, such as caning or intricate layering, ensure that your chosen cutter can accommodate those methods appropriately. Integrating these considerations will ultimately enhance your crafting experience and the quality of your finished polymer clay creations.
Techniques for Using Polymer Cutters Effectively
Effectively utilizing polymer cutters requires a blend of skill and understanding of the material involved. The preparation of polymer clay is the first crucial step. Ensure that the clay is adequately conditioned by kneading it until it achieves a soft, pliable consistency. This process not only enhances the workability of the clay but also eliminates air bubbles, which can interfere with the cutting process. Once properly conditioned, the clay should be rolled out to a uniform thickness that is compatible with your specific cutter design.
When using the polymer cutters, applying the right pressing technique is essential. Position your cutter over the clay and press down firmly, ensuring that the edges are adequately engaged in the material. A steady, even pressure is key to achieving clean, precise cuts. Avoid using excessive force, as this can lead to distortion of the shapes or messiness along the edges. A rocking motion while applying pressure can sometimes assist in cutting through thicker clay, providing a more refined finish.
To achieve clean cuts, it is beneficial to regularly dust the cutter’s edge with cornstarch or talcum powder. This step prevents the clay from sticking to the cutter, which can result in uneven shapes. Additionally, if the cutter becomes stuck, gently wiggle it side to side instead of pulling directly upwards, as this can help release the cut clay with minimal tearing.
Common issues may arise when working with polymer cutters, such as rough edges or incomplete cuts. If you find that the edges of your shapes are not as smooth as desired, consider using a sharp blade to trim them post-cutting. By maintaining these techniques and troubleshooting tips, artisans can ensure successful outcomes in their polymer clay projects, leading to enhanced creativity and satisfaction with their work.
Maintenance and Care for Polymer Cutters
To ensure the longevity and functionality of polymer clay cutters, proper maintenance and care are essential. These tools, which are widely utilized for creating various shapes and designs in polymer clay crafting, can benefit significantly from a consistent cleaning and storage routine. Regular maintenance not only preserves the cutters’ quality but also enhances the overall crafting experience.
Cleaning polymer cutters should be the first step in the care process. After each use, it is advisable to rinse them under warm, soapy water. A soft brush or cloth can be utilized to gently scrub away any residual clay. Avoid using abrasive materials or harsh chemicals, as these can damage the cutter’s surface. Rinse thoroughly and dry them completely with a soft towel to prevent water spots or any possible rusting, particularly if the cutters are made from metal.
In terms of storage, it is essential to keep polymer clay cutters in a dry, cool environment. A dedicated storage box with a soft lining is ideal to prevent scratching and to keep them organized. Laying them flat can help avoid bending, which could affect their cutting precision. It is also prudent to store them away from direct sunlight and extreme temperatures, as these conditions can warp the plastic or dull the edges of metal cutters.
Moreover, it is important to avoid particular practices that could potentially harm the cutters. For instance, do not use them on non-polymer materials, as this could lead to dulling the cutting edges. Additionally, avoid letting polymer clay dry on the cutters for extended periods, as this can make cleaning more difficult. By adhering to these maintenance and care guidelines, creators can ensure their polymer clay cutters remain in optimal condition for crafting, allowing for a seamless and enjoyable creative process.
Inspiration from Polymer Clay Artists
Polymer clay artists have been at the forefront of innovation in the crafting community, utilizing an array of tools, especially cutters, to transform basic elements into complex designs. Notable artists like Angie Scarr, known for her whimsical creations, often emphasizes the importance of using cutters to create intricate shapes that serve as foundational elements in her work. She remarks, “Cutters enable me to maintain consistency while allowing for endless creativity.” Her designs frequently feature detailed patterns and shapes that highlight how essential these tools can be in achieving both precision and artistic flair.
Another influential figure in the polymer clay sphere is Lisa Pavelka, whose vibrant and textured works serve as a testament to the versatility of polymer clay. Pavelka emphasizes the impact of different cutter designs, stating, “The right cutter can change the entire direction of a project.” Many of her pieces showcase a mixture of cutter shapes, from geometric to organic forms, illustrating how these tools open up new possibilities for creativity. Her approach demonstrates that cutters are not merely functional tools but instruments of artistic expression.
Additionally, we can draw inspiration from Danielle Wilkerson, whose elegant and minimalist designs often highlight the beauty of simplicity. She advocates for a careful selection of cutters, focusing on how each shape can complement the overall aesthetic of her projects. “I often experiment with negative space created by cutters,” she explains, pushing the boundaries of traditional polymer clay art. Her innovative use of negative space showcases the importance of integrating functional tools into one’s artistic vision.
These artists serve not only as sources of inspiration but also as reminders of the crucial role that polymer cutters play in shaping artistic expression within the polymer clay realm. By exploring their techniques and philosophies, readers may find new directions for their own creations.
What’s Next in the World of Polymer Cutters?
The landscape of polymer cutting tools is poised for significant evolution, driven by advancements in technology and innovative crafting techniques. As we look to the future, various trends are likely to shape the polymer cutter market and influence the way artists work with polymer clay. One notable direction is the integration of more sophisticated materials in the production of polymer cutters, ensuring enhanced durability and precision. Manufacturers are exploring composite materials that reduce wear over time, allowing for more intricate designs and consistent results.
Another trend on the horizon is the incorporation of smart technology into polymer crafting tools. We are beginning to see digital cutting tools that can connect wirelessly to design software, enabling creators to produce custom shapes and sizes with remarkable accuracy. This innovation not only simplifies the cutting process but also opens up endless possibilities for personalization in polymer clay projects. As these technologies advance, we can expect a more streamlined workflow that caters to both amateur and professional crafters alike.
Moreover, the industry is seeing a shift toward environmentally friendly crafting practices. As awareness of sustainability increases among consumers, manufacturers are likely to respond by creating polymer cutters from recyclable and sustainable materials. This not only meets the ecological concerns of modern artists but also promotes a more responsible approach to crafting.
As we move forward, stay tuned for our next blog post, where we will delve deeper into these emerging trends and technologies in the realm of polymer cutters. The future of polymer clay crafting is bright, full of innovation and creativity, and we invite you to join us as we explore these exciting advancements together.